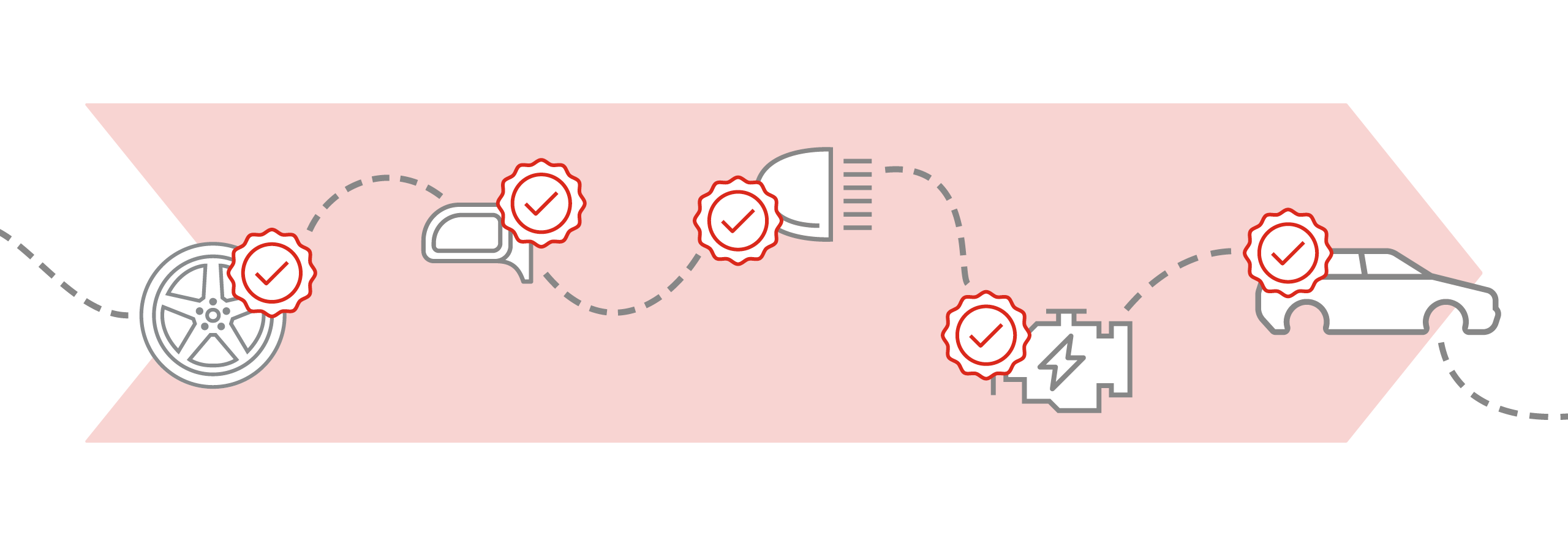
CURRENT STATUS OF HOMOLOGATION FOR SERIES VEHICLS: REQUIRED EVERYWHERE - BUT ALSO DIFFERENT EVERYWHERE
The fact that cars must comply with a seemingly overwhelming number of regulations before they are put on the market is not specific to Europe. Vehicles everywhere need to be certified in accordance with homologation requirements. In China, currently the world's largest market in the automotive industry, such guidelines are also in place. In many respects, these are based on European regulations. Nevertheless, they differ in key aspects from the applicable regulations in Europe or the USA.
The EU Framework Directive 2018/858/EU forms the basis for all relevant regulations a vehicle must comply with to be approved in EU countries. However, in addition to simply obtaining type approval, there are also various legal requirements that must be met – for example, regarding bans on substances that may not be used as raw materials or in production. In individual EU member states, national regulations may also apply in individual cases that affect the approval process as such.
COMPANY AND FACTORY CONFORMITY: REQUIREMENTS FOR AN OEM TO HOMOLOGATE VEHICLES FOR THE EU
Long before the vehicle is actually homologated for market entry, the manufacturer must undergo an examination of the requirements. The aim is to prove that the OEM is able to produce the vehicles in such a way that the quality requirements are always met.
This means that the manufacturer must have established appropriate quality management systems. For example, in accordance with the specifications of ISO standard 9001 or IATF 16949. These ensure that not only the complete vehicle itself is correctly designed and developed to comply with the regulations valid at the time of homologation. The manufacturer must also ensure to the certifying authority that the vehicle can be manufactured to operate correctly over the entire product life cycle, over the entire model life. It makes sense if not just the regulations valid at the time of homologation are fulfilled, but also future regulations that will come into law during the production period. The OEM must therefore be aware of planned legal changes in advance.
The first step for the certification of the manufacturer is the initial assessment of the manufacturer and the production site. The OEM must also demonstrate having a production control plan that conforms to the regulations and ensures ongoing compliance with the relevant criteria. The correct implementation of the updates required during the product life cycle must also be ensured.
If all these points are met and verified, the relevant authority – such as the German Federal Motor Transport Authority, for example – confirms the initial assessment. In any case, a plant audit is also carried out in advance. This audit is mandatory, even if there are several production facilities for each plant. Representatives of the relevant authority inspect the factory in detail on site, from the implementation of the required quality management systems to proof of the training of production employees.
INDIVIDUAL APPROVAL PROCEDURES FOR DIFFERENT SYSTEMS: THE SYSTEM TYPE APPROVALS
Once the manufacturer certification process has been completed, the next step is to obtain system approval for individual sub-systems. For example, compliance with the applicable specifications for crash behavior, or the requirements for the braking system, the lighting equipment or prescribed assistance systems must be verified as an individual system approval.
In principle, the OEM can choose which European authority to apply to for homologation. It is entirely possible to verify different systems with different authorities in different countries and with the help of different technical services. Usually, the respective authority will nominate one or more technical services to carry out the relevant inspection on behalf of the authority. For a new Chinese OEM wishing to enter the EU market, it is often difficult to decide which country - i.e. which authority - to choose for the system type approval and which technical service provider is the most suitable.
ONE STEP AHEAD OF THE GOAL: THE COMPLETE VEHICLE TYPE APPROVAL
A complete vehicle type approval can only be applied for when all system approvals have been acquired – that is, when conformity has been proven for all systems. The complete vehicle type approval can only be obtained when the finished vehicle can be subjected to an assessment at a stage of development corresponding to the later series production.
Here, too, it is up to the manufacturer to decide in which EU country he wants to obtain the type approval. If it is granted in one EU country, it is valid throughout the entire EU. All countries of the corresponding EU agreement are authorized to approve a vehicle or even individual components. Furthermore, they are obliged to recognize the approval issued in another member state.
However, if, for example, the manufacturer has obtained approval for a vehicle type with one approval authority in one EU country and wishes to register a new vehicle type with another approval authority in another EU country, it must again verify the regulatory conformity of the company and the manufacturing plant in that country.
REQUIRED APPROVAL AND REGISTRATION WITH NATIONAL AUTHORITIES
If the complete vehicle type approval is granted in an EU member state, a type approval number is issued in accordance with EU Regulation 2018/858/EU. The vehicle manufacturer or general importer can use this to gain national approval in the respective EU country. The vehicle type is entered in the respective national approval database. The end customer can only get the registration of his vehicle via this number.
ACCELERATED MARKET LAUNCH THROUGH LEAN TESTING DURING DEVELOPMENT
In the competitive automotive industry, it is clearly in the OEM's interest to enter the market with a new vehicle type as quickly as possible. But the necessary homologation process takes time. It usually takes around six months from the time the fully developed vehicle is made available for testing until it is granted a complete vehicle type approval. This time, which is required by the authorities involved, cannot be shortened very much, although the time required to prepare for the final homologation can certainly be reduced.
The most important tools for this are lean testing and virtual development. Many system approvals can already be carried out in the virtual development phase. This saves time and resources for prototype construction. At Magna, this approach is called lean testing, where development testing and homologation testing are combined. This means that the same pre-series vehicles on which the final development tests are conducted are also used for the necessary homologation tests.
This is possible if the virtual development has already reached such a high level of maturity that the last prototype generation is no longer necessary. Specifically, the final development tests are conducted in conjunction with the final technical service so that the development test can also be used for homologation. This is a good and proven way of saving an entire generation of vehicles, which not only speeds up the market launch, but also helps to avoid needlessly high costs.
COLLABORATION WITH AN EXPERIENCED DEVELOPMENT PARTNER AVOIDS DETOURS AND UNNECESSARY EXPENDITURE
It is highly beneficial to work with an experienced development and homologation partner in Europe who has already applied and put their expertise into practice in many projects. A comprehensively competent development partner with a powerful and universally competent homologation team is very familiar with all current regulations and those that will take effect in the foreseeable future. They can thus provide the OEM with comprehensive support in all homologation matters.
This allows a Chinese OEM to ensure that the vehicles produced meet current and future safety and environmental standards. Ideally, the European development partner provides this support as an integral part of the vehicle development, so that the finished vehicle type can be marketed worldwide.
GLOBALLY RECOGNIZED HOMOLOGATION SAVES TIME-CONSUMING REDEVELOPMENT
In general, all systems are designed in a way that complies with more than just the UNECE regulations. They have been recognized by a number of non-EU countries or adopted in their national regulations. The requirements of other markets with differing regulations can also be considered from the outset. This eliminates the need for time-consuming and cost-intensive subsequent developments if the vehicle type is to be launched in additional markets after the start of series production.
However, some markets require a different approach. In the USA, for example, there is no cooperation with technical services to check conformity with the applicable regulations. Instead, the manufacturer uses a self-certification process in which the manufacturer itself confirms compliance with the statutory regulations and is therefore 100 percent responsible for its own compliance.
CHALLENGES IN THE HOMOLOGATION OF CHINESE VEHICLES
Incidents such as those that occurred almost 20 years ago, when a Chinese SUV attracted attention with poor results in crash tests and could therefore only be sold with individual registration at best, are hardly even imaginable today. Chinese OEMs are now at a globally competitive level when it comes to the hardware quality of their vehicles. In this respect, negative surprises in the physical homologation tests are no longer to be expected.
Nevertheless, even in the final phase of development, functions may not meet the requirements in detail. However, this usually involves improvements at software level, which can then be carried out at short notice and without component changes. Software changes that are necessary to meet additional customer requirements but were not originally taken into account can also pose new challenges.
Here, too, the Chinese OEM can rely on a competent European partner to support the entire development process. They can not only identify the necessary modifications, but also implement them promptly to avoid the risks of non-compliance during the final homologation.
Stay connected with Inside Automotive!
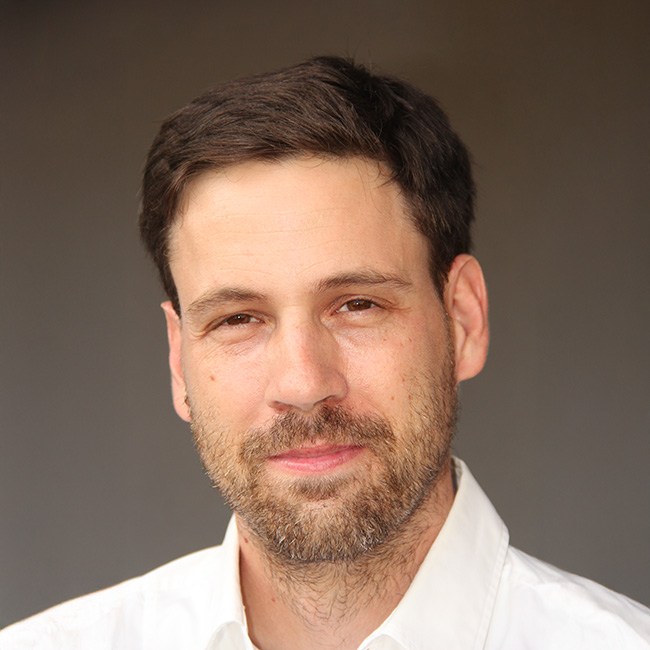
We want to hear from you
Send us your questions, thoughts and inquiries or engage in the conversation on social media.
Related Stories
Stay connected
You can stay connected with Magna News and Stories through email alerts sent to your inbox in real time.